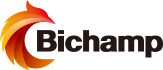
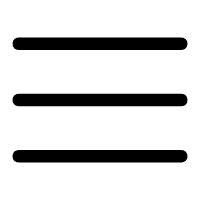
Your location: > About > Sustainable Development
The 20th Lean Improvement Tour was held.Recently, the 20th Lean Improvement Tour was held in Bichamp. This issue showcases improvement cases currently being carried out by various departments and has achieved good results. Eight improvement points were set up, involving R&D, Information Technology, Import & Export, carbide, composite, and saw band workshops.
Company leaders led all department heads, section heads, and lean department officers. A total of more than 40 people gathered from the carbide workshop to listen to each publisher's project explanation in detail and discuss the following improvement ideas and methods with the actual situation on site.
The first improvement point is CB laser cutting head and tail waste improvement, which workshop employee Li Yong explained. This improvement effectively reduces the production cost, which is typical of a significant return on a small investment. After modifying the equipment fixture and adjusting the operation standard, the processable material head and material tail per strip were reduced from 1.8m to 0.5m before, which can save more than 40,000 yuan of material cost per year according to the current production capacity.
The composite workshop is the improvement of the S-bend inspection method of composite material. This improvement is exquisite and ingenious, cohesive workshop technicians' efforts, breaking the original stopping-cutting manual inspection method to achieve S-bending online automatic detection. Not only can it reduce the inspection time by 40 hours per month, saving more than 230,000 yuan per year in material cost loss due to cut-off inspection, but it also ensures the accuracy and validity of the inspection data, which is convenient for data traceability and analysis later.
Production of online detection and the automatic alarm is the direction of the company's development, and it is the critical work that the Information Technology Department has been working on. To realize the automatic control of the temperature of the quenching and tempering production line, the Information Technology Department has carried out a 1-year improvement of the temperature control of the metallographic room.
The company utterly developed and implemented this improvement, which realized the automatic collection and centralized control of equipment process temperature. After the modification, the system operated stably and reliably, which not only reduced the monthly operation time by 278 hours, equivalent to 120,000 RMB/year, but also reduced the project outsourcing cost by more than 400,000 RMB, ensured the reliability of data to avoid possible misoperation, and made a brand-new suggestion on the later maintenance and function improvement of the system. The developed temperature control system was praised by everyone for its friendly interface, simple and effective operation, and reliable error-proof.
Finally, after the judges' careful evaluation, "Improvement of Sino-Russian logistics," explained by Guo Huizhi of the Import and Export Department, won the first prize, "Improvement of eliminating the misaligned teeth caused by "falling knife place" by Li Zhong of Saw Belt Workshop and "Improvement of the remote control system in the metallographic room" by Liu Rongjie of Information Technology Department won the second prize, "Improvement of S-bend detection method" by Yang Rongzhai of Composite Workshop and "Improvement of S-bend detection method" by Saw Belt Workshop won the second prize. The improvement of S-bend inspection method" by Yang Rongzhai of the compound workshop and "comprehensive packing improvement" by Xie Qizhi of saw belt workshop won the third prize.